Introduction
Comminution is the most energy-intensive process in the mine value chain; and along with the mine loading and hauling fuel, it also represents the most OPEX-intensive costs of an operation. However, the impact of comminution in the downstream process goes beyond the energy consumption and the consumables economics. Comminution performance metrics such as mill throughput and final grind size are drivers for flotation recovery.
As drivers of flotation recovery, both mill throughput and final grind size need to be kept as stable as possible during the operation through process control. Figure 1 shows how large the variations in final grind size, as a result of variations in throughput, can result in different flotation recovery in a large Lead-Zinc operation.
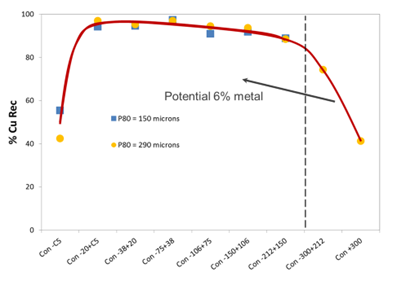
SAG Mill Operating Stability
Mill throughput and final grind size are drivers for flotation recovery. Therefore, grinding circuits should operate as stable as possible to minimize variations in flotation recovery.
There are a few approaches that can help achieve grinding circuit operating stability, the most common being;
- Process control; and,
- Ore blending.
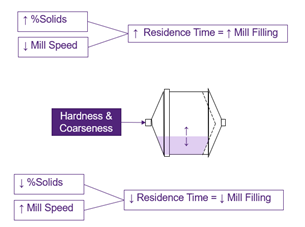
Variables to Stabilise SAG Operation
Process control uses variables such as SAG mill speed and %Solids to accommodate the variations in ore competency and coarseness. However, large variations in ore competency often exceed this operating flexibility resulting in variable mill throughput and final grind size, negatively affecting flotation recovery.
Figure 2 shows the two variables that are used in process control in an attempt to stabilise SAG mill operation in terms of mill throughput and final grind size.
The variables include;
- Millspeed (controlled ising a variable speed drive); and,
- Density control
As the feed characteristics for ore competency and coarseness change, the residence time will also change. Typically, fine and soft ores will have shorter residence times in the mill than coarser and harder ores. Also, the residence time in the mill will often dictates how much new fines are generated by abrasion breakage within the charge. Operating variables such as mill speed and density can be adjusted to accommodate the variations in residence time and hence in SAG mill filling, aimed at bringing stability to the process. High % solids and lower mill speeds will promote longer residence times in the SAG mill, resulting in higher mill fillings, whereas lower % solids and high mill speeds will promote shorter residence times in the SAG mill resulting in lower mill fillings. Other variables such as throughput can also be manipulated to stabilise SAG power but not final grind size as the throughput variations themselves are the cause of an unstable operation.
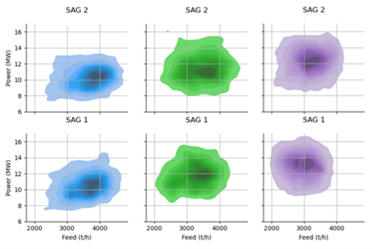
Ore blending requires a comprehensive ore characterisation campaign across the deposit. With this information sites will be in a better position to narrow down the ore characteristics fed to comminution, bringing stability to throughput, final grind size and flotation recovery.
Figure 3 shows the variability in SAG mill power and throughput in a large Lead-Zinc operation over five years of continuous operation for a range of ore domains. These variations in mill throughput and SAG mill power draw were registered as a result of large variations in ore competency within individual ore domains causing variations in flotation performance, despite a rigorous process control.
Therefore, the next level of process stability is not in process control but in the ore domaining (geometallurgy) and in the ore blending; if site has the capabilities to identify the softest and hardest materials to AG/SAG milling ahead of time through a routine and meaningful ore characterisation.
SAG Mill Filling
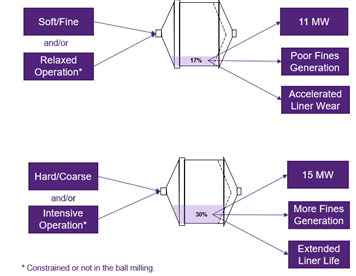
Throughput and Fines Generation
One of the main characteristics of SAG mills is their grate discharge mechanism. That means rocks in the mill charge stay inside the mill until they reach a size that can pass through the grate size or pebble aperture. Therefore, mill throughput is not determined by how much tons are fed to the SAG mill, but by how much material can be discharged by the mill. SAG mill filling is also a driver for throughput, power draw and fines generation. Hence the importance of tracking it in real time.
SAG mill filling is driven by the ore competency to SAG milling, i.e. Axb value from JKDWT or SMC test. The more competent to SAG milling the ore is (lower Axb value), the longer the residence time resulting in more fines generation. The less competent to SAG milling the ore is (higher Axb value), the shorter the residence time resulting in poor fines generation. SAG mill filling is also important as it drives SAG mill power draw, throughput, and fines generation (Powell, 2009) as illustrated in Figure 4. Other advantages of operating with a high mill filling is that liners will be more protected against direct impact with the steel media, extending the liner lifetime. With low mill fillings, liners are more exposed to direct impact to the steel media, accelerating liner wear.
Figure 5 shows the comparison of key comminution circuit performance metrics between two plant trials, Trial 1, and Trial 2, to illustrate the importance of monitoring SAG mill filling and its impact on final grind size and consequently on flotation recovery. Trial 2 overall contained finer and softer material than Trial 1. Each trial involved 12 hours of continuous operation. The finer and softer material of Trial 2 resulted in shorter residence time in the SAG mill, which was reflected in a lower mill filling, as inferred by a soft sensor (JKMillFIT), and thus in a lower SAG mill power draw. The shorter residence time in the SAG mill during Trial 2, resulted in a poor fines generation the SAG mill which was ultimately reflected in a coarser final grind size, negatively affecting flotation recovery.
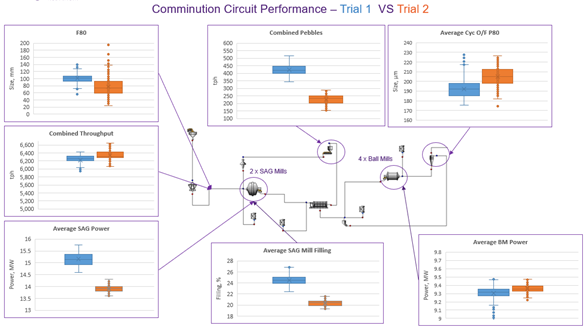
Monitoring SAG mill filling in real time is therefore key to all operations to ensure there is enough residence time for a healthy generation of new fines in the SAG mill, alleviating the work for the ball mills to achieve the target grind size. As a driver for mill power draw, SAG mill filling is also key to maximise SAG power utilisation. SAG mills are often operated very conservatively in the absence of reliable online information on the actual operating limits.
Monitoring SAG mill filling in real time is challenging based on available instrumentation in the SAG mill. SAG mill instrumentation often includes bearing pressure readings. Bearing pressure measures the response to mill weight in kilopascals (kPa), which includes both the charge weight and the mill liners weight. It is hard to differentiate between the two if mill liner wear is not closely monitored. The error in estimating mill filling can be huge when using an uncalibrated bearing pressure and not correcting for the liner mass loss as they wear.
This technical bulletin is based on a paper presented at the Procemin-Geomet conference in Chile.
JKTech offers geometallurgy support through consulting and test work. Please contact us to learn more about our geometallurgy capabilities.
References
M.S. Powell, A.P. Van der Westhuizen, A.N. Mainza. Applying grinding curves to mill operation and optimisation. Minerals Engineering. Volume 22, Issues 7-8, June-July 2009, Pages 625-632.
Morell, S, 1993. The prediction of power draw in wet tumbling mills. Julius Kruttschnitt Mineral Research Centre. Department of Mining and Metallurgical Engineering. University of Queensland.
Morrell, S, 2008.A method for predicting the specific energy requirement of comminution circuits and assessing their energy utilisation efficiency, Minerals Engineering, 21(3).
David D. (2013). Is an 80th Percentile Design Point Logical?. Metallurgical Plant Design and Operating Strategies (MetPlant 2013) 15 – 17 July 2013, Perth WA.
Weier M. (2023). Insights Into Rock Breakage Experience for Over 30 Years. (SAG Conference 2023) 24 – 28 September 2023, Vancouver.