The first step to understanding and quantifying the impact of blast hole deviation on blasting efficiency is to measure. It is understood that there are significant cost, time and downstream productivity implications when deviated blast holes are not factored into the quality assurance and control processes. Blast hole deviation is traceable to rock mass properties, drilling parameters, drilling setup or drilling equipment error and collaring error.
Some of these error sources are difficult to predict or control necessitating measurement of the drillhole deviation before blasting is carried out.
A reason why we should measure blast hole deviation is to understand and minimise ore loss and dilution through over-break and under-break. Over-break being when the resulting void is larger than intended and under-break being when the resulting void is smaller than intended.
Figure 1 is an example of underground stope. The dark blue lines represent the design holes, and the light blue holes represt the ‘as measured’ actuals.
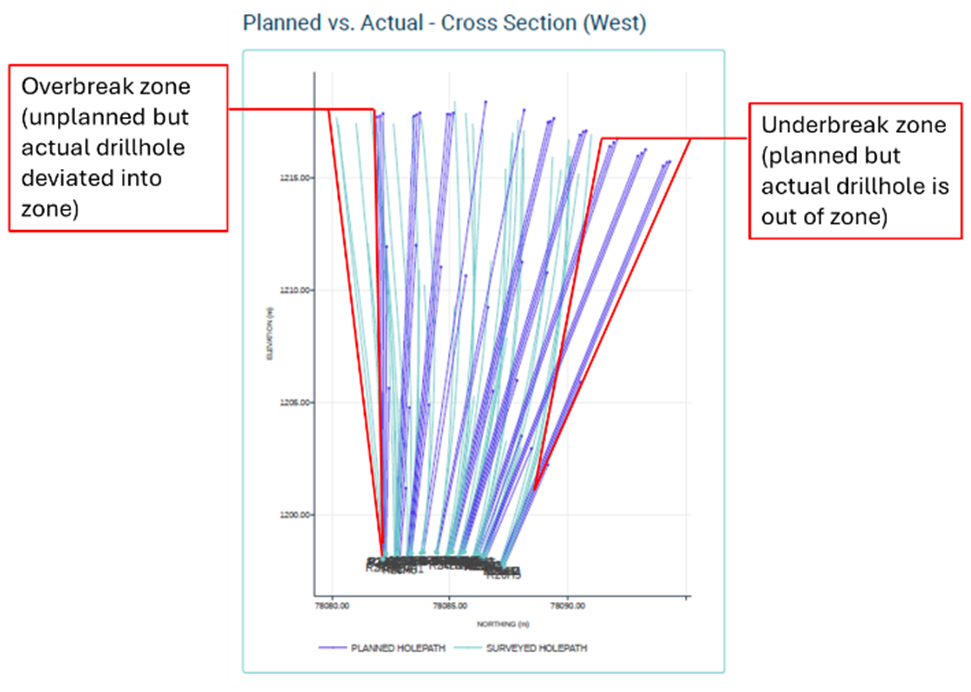
There is a large discrepancy between the design and actual which will result in significant over-break and under-break. Therefore, leading to ore loss and dilution. An example of significant over-break is shown in Figure 2.
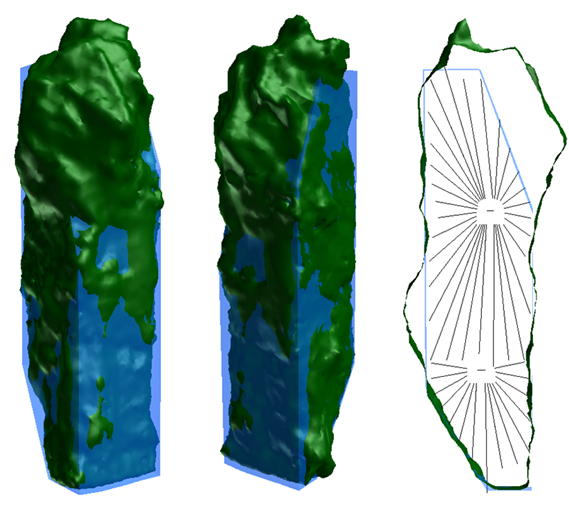
New Measurement Technology
In underground mines, surveying overhead drill holes (up-holes) in the back of the drive requires the use of an elevated work platform (e.g. Integrated tool carrier basket or scissors lift) to access the blast hole collar in order to deploy the survey instrument into the hole (Figure 3). Elevated work platforms are vital for multiple tasks in an underground operation and are typically not readily available for blast hole surveying which is often ranked low in priority. There are other constraints such as cost, availability of trained personnel and safety that limits the use of this workflow for blast hole surveying. Additionally, there are generally undeveloped processes for measuring blast hole deviation or lack of awareness of its role in blasting outcomes.
Another major limitation of most of the survey systems available today is that they require an established control point or an external input to initialize the survey process.
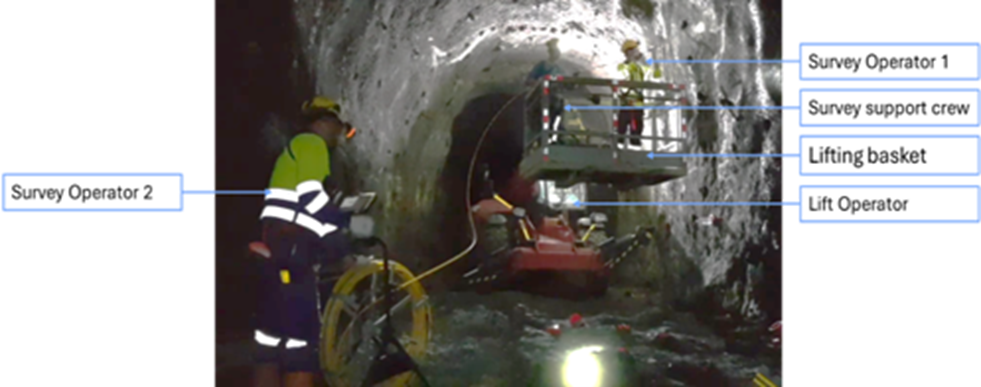
Both of these limitations are eliminated when a North-seeking gyroscope system is utilized for blast hole surveying. The newest generation North-seeking gyroscopic based blast hole surveying system OMNIxBOLT (Imdex Technology Limited) is the first measurement system where both up-holes and down-holes can be accurately surveyed from ground level without the requirement for an elevated work platform, saving on personnel and equipment costs.
System Accuracy
There is a long list of inputs which can cause inaccuracy to the results. Some of these inputs include:
- In-hole tool roll
- Gyro over-rate
- Data acquisition speed
- Incorrect collar vector measurement
- Incorrect collar position survey
- Operator error
- Calibration
- Centraliser design
- Inherent probe inaccuracy
Blasthole deviation measurement systems have often been designed to be used in exploration scenarios which provide relatively controlled conditions. Exploration holes are often cased, therefore smooth and the gyroscope is lowered down the hole mechanically. In comparison, internal blast hole surfaces are often rough, and the gyroscope is deployed manually. This results in relatively uncontrolled conditions for blast hole surveying. As such, the accuracy of the system needs to be considered in place of the ‘probe accuracy’ as stated in the gyroscope specifications. An example of how a component of the system can cause a significant inaccuracy is as follows.
A test was conducted with two different centraliser types (design 1 and design 2). In total 20 runs were done in total. All runs using both the centraliser designs are shown in Figure 4. There are results which stray up to 300mm from the centroid of most runs.
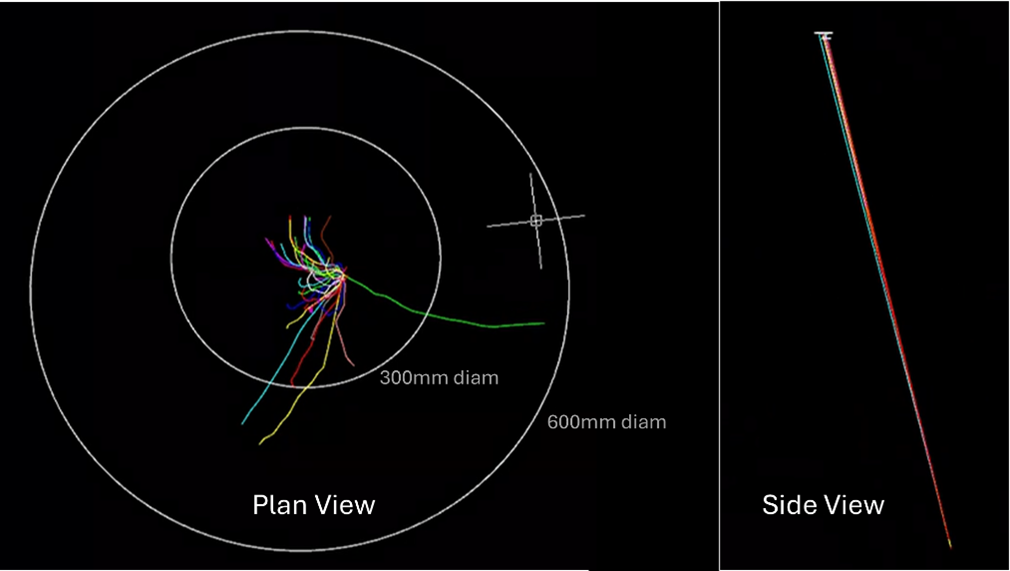
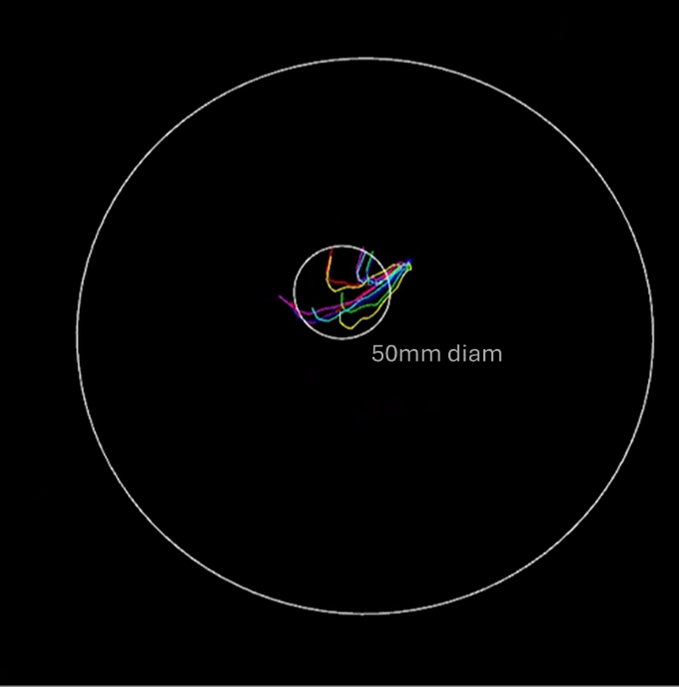
Removing the results from centraliser design 1 and displaying only design 2 gives the result in Figure 5.
With centraliser design 2 all runs fall in a tight group which is an acceptable result. Centraliser design 1 yields an unacceptable result.
This result illustrates that one component can have a large impact on overall accuracy and highlights the need to understand system accuracy more so than probe accuracy.
This technical bulletin was based on a presentation presented at Fragblast 14 Conference in Antalya, Turkey.
JKTech offers blasting support through consulting and test work. Please contact us to learn more about our offerings.