Accurately predicting the future performance of a concentrator, especially mill throughput, is crucial in mine planning. These predictions support various aspects of the mine value chain, including resource definition, mine development, production optimisation, cost control, and concentrate logistics and sales. They also play a vital role in business risk mitigation and inventory management.
The methods for making these predictions vary widely within the industry, ranging from simple fixed daily throughput assumptions to detailed ore characterisation campaigns utilising multiple simulation models. Typically, compromises must be made to balance prediction accuracy versus costs in a way that is fit for purpose for the business.
One common method when developing throughput models is to develop ‘proxy’ relationships – using comparatively cheaper (and more readily available) measurements like geochemical assays to predict the ore competency parameters (which measure the ore resistance to breakage for different breakage mechanisms) from full-scale comminution tests (e.g. JKDWT, SMC test, BWi test). This is in contrast to first developing a relationship between a proxy and the ore competency parameter based on test work on the relevant ore domains. JKTech has many case studies available where this approach has provided cost effective, accurate predictions. Therefore, in some instances, it may be reasonable to skip the comminution test work step and try to predict future performance based on these ‘proxies’ without correlating to comminution test work results. For example developing a model directly linking mill feed grade/s and historical mill throughput for an operating concentrator.
However, this is not always the case as orebodies are not created equally and can behave differently, even between domains of the same orebody. In some cases, developing a throughput model without comminution test work can produce results with wildly different quality of predictions, even when the main ‘proxy’ is the same between both approaches.
Example
In this example, the throughput models from a site’s geometallurgy program are compared. The first modelling approach (Fig 1 and 2) does not use comminution test work results in the model and directly links head grade to predicted throughput. While this model may or may not be significant, has an extremely low coefficient of determination (R2) value, meaning that most of the variance is not being captured from the relationship. It can also be seen from the parity chart in Fig 2 that there is no meaningful relationship between the two variables.
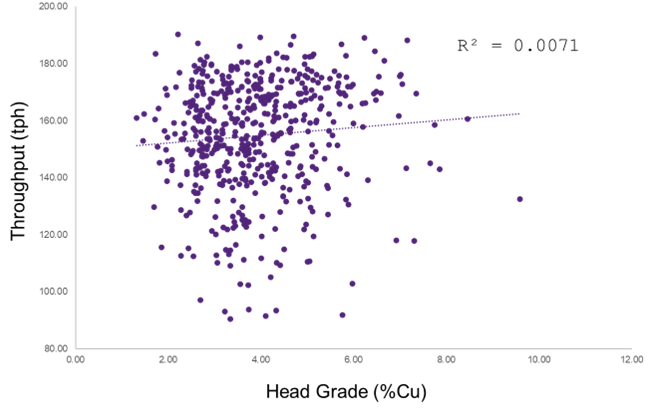
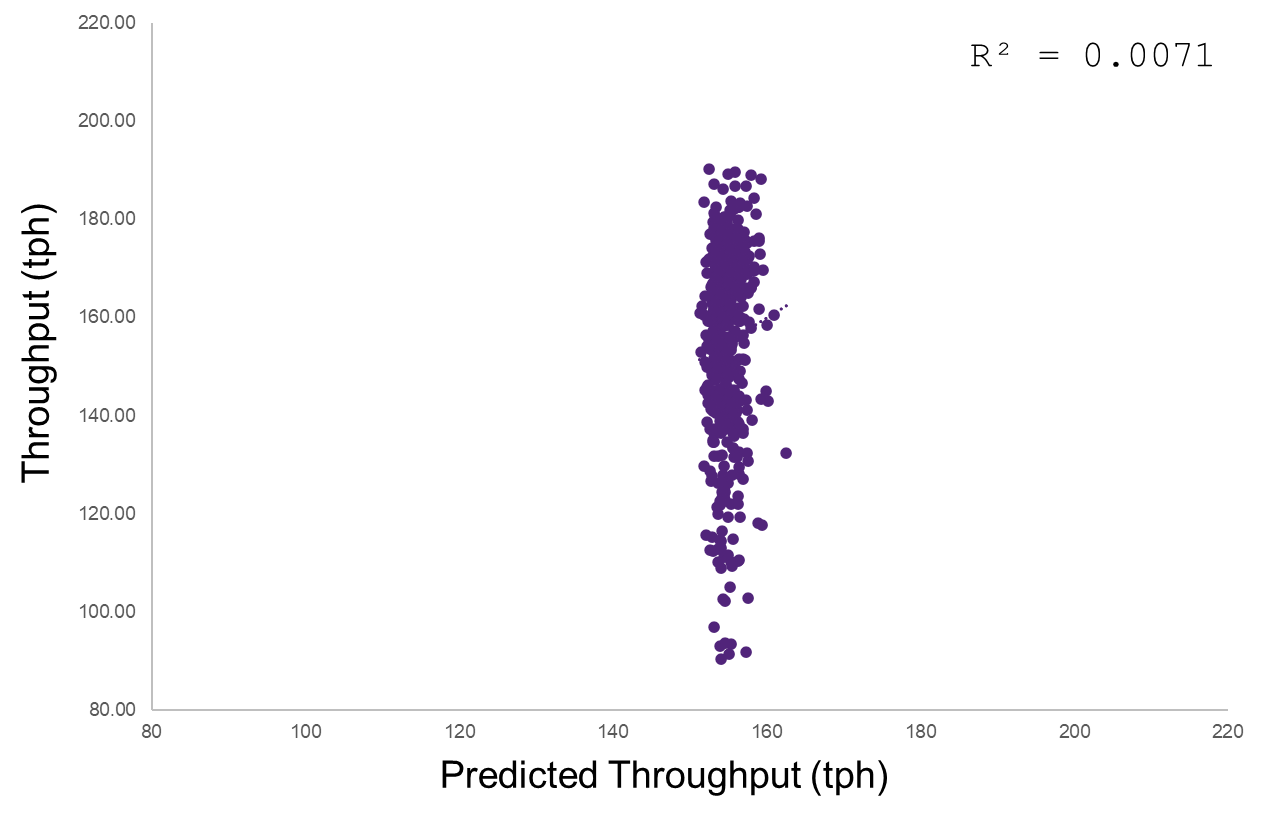
The second modelling approach (Fig 3) utilises comminution test work. It still utilises head grade in the model but the head grade is first used to predict the equivalent ore competency (e.g. Axb, BWi) based on concurrent comminution test work. When comparing the parity graphs for the first (Fig 2) and second (Fig 3) modelling approach, the second modelling approach has better agreement. As such, it was deemed fit for purpose to be used in production planning.
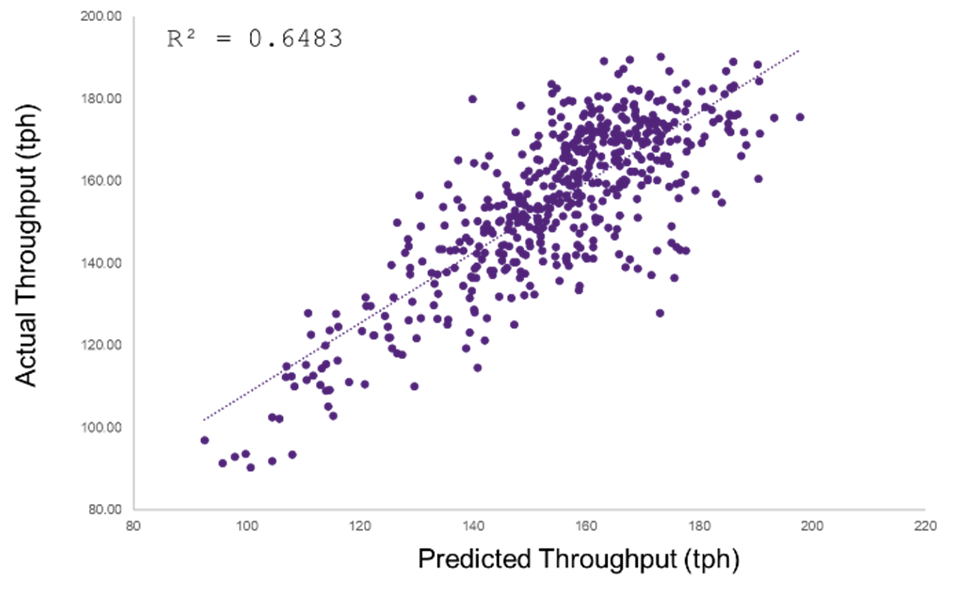
So, what was the difference?
Key differences are;
- The relationship between the ‘proxy’ and ore competency was non-linear (which is common);
- The plant had variable operating parameters, such as feed density, mill power draw etc that have a statistically significant effect on predicted throughput and should be included in the model; and,
- The feed to the plant had varying particle size distribution, as well as the circuit product, and how these influence mill throughput can be complex and was only captured by including them in the model.
Instead of directly fitting the ‘proxy’ (head grade), modelling approach used first fitted to ore competency parameters from full-scale tests. These parameters were then used in specific energy equations, accounting for much of the remaining variance and significantly improving the regression fit. This approach allowed site to reach their desired balance of reducing test work cost while developing (and maintain) a model with an acceptable accuracy.
This technical bulletin was based on a presentation presented at the AusIMM NSW Central West Minerals Forum in Dubbo, Australia.
JKTech offers geometallurgy support through consulting, test work and training. Please contact us to learn more about our offerings.