JK Mine-to-Mill:
Antamina Copper and Zinc Mine
The Antamina JK Mine-to-Mill assessment demonstrates that blast fragmentation is just one of the levers that can be adjusted to optimise the mine value chain process integration. This integrated assessment has recognised a total US$24m in value, three times what would normally be expected.
A JK Mine-to-Mill assessment costs $500k over four to six months to complete. Upon implementation, the results represent a less than one month payback
At Antamina we identified:
3x
potential operation margin improvement
over blasting optimisation alone
66%
of improved value delivered
through ore blending
1 week
to pay back JK Mine-to-Mill fees
once fully implemented
JK Mine-to-Mill
JK Mine-to-Mill incorporates two additional levers of process integration, that can be as, or more, important than blast fragmentation. They are ‘ore characterisation’ and ‘ore control’.
The various levers for process integration are often addressed separately at operations rather than holistically. And not exhaustively enough, as measurements are either not sufficiently available or simply not suitable to effectively improve current practices.
'Ore characterisation' is essential to ensure consistent ore characteristics are fed to the processing plant, bringing stability to throughput, grind size and flotation recovery. Large variations in ore hardness often exceed SAG mill operating flexibility, inevitably resulting in an unstable grind size and highly variable flotation circuit, leading to losses in recovery. The latest approach to flexibility and a steady grind size is not in process control but in ore blending if the site has the capability of identifying the hardest and the softest materials through routine and meaningful ore characterisation. In addition to plant stability and consistent metal recovery, meaningful ore characterisation will allow improvement of mine planning with more accurate throughput forecasting models.‘Ore control’ is key to maximising productivity. As comminution is the most energy-intensive process in the mine value chain, minimising ore loss and dilution through advanced ore control becomes the key to unlock significant opportunities for operations, including enhanced head grade and metal recovery.
History
The Mine-to-Mill philosophy, originally developed at the Julius Kruttschnitt Mineral Research Centre (JKMRC) in the early 1990’s, focuses on blast fragmentation as the main lever for process integration, debottlenecking SAG mills and creating room for concentrator throughput increase.
At JKTech, this philosophy has evolved over the years to include additional levers of process integration to suit the needs and realities of any mine site, because not all comminution circuits are constrained by the SAG mill, and hence not all sites will benefit from blasting more aggressively. This includes new technology such as JKMillFIT and JKVBOC, together with alternative ore characterisation methods.
What We Found at Antamina: Ore Characterisation Data is Imperative
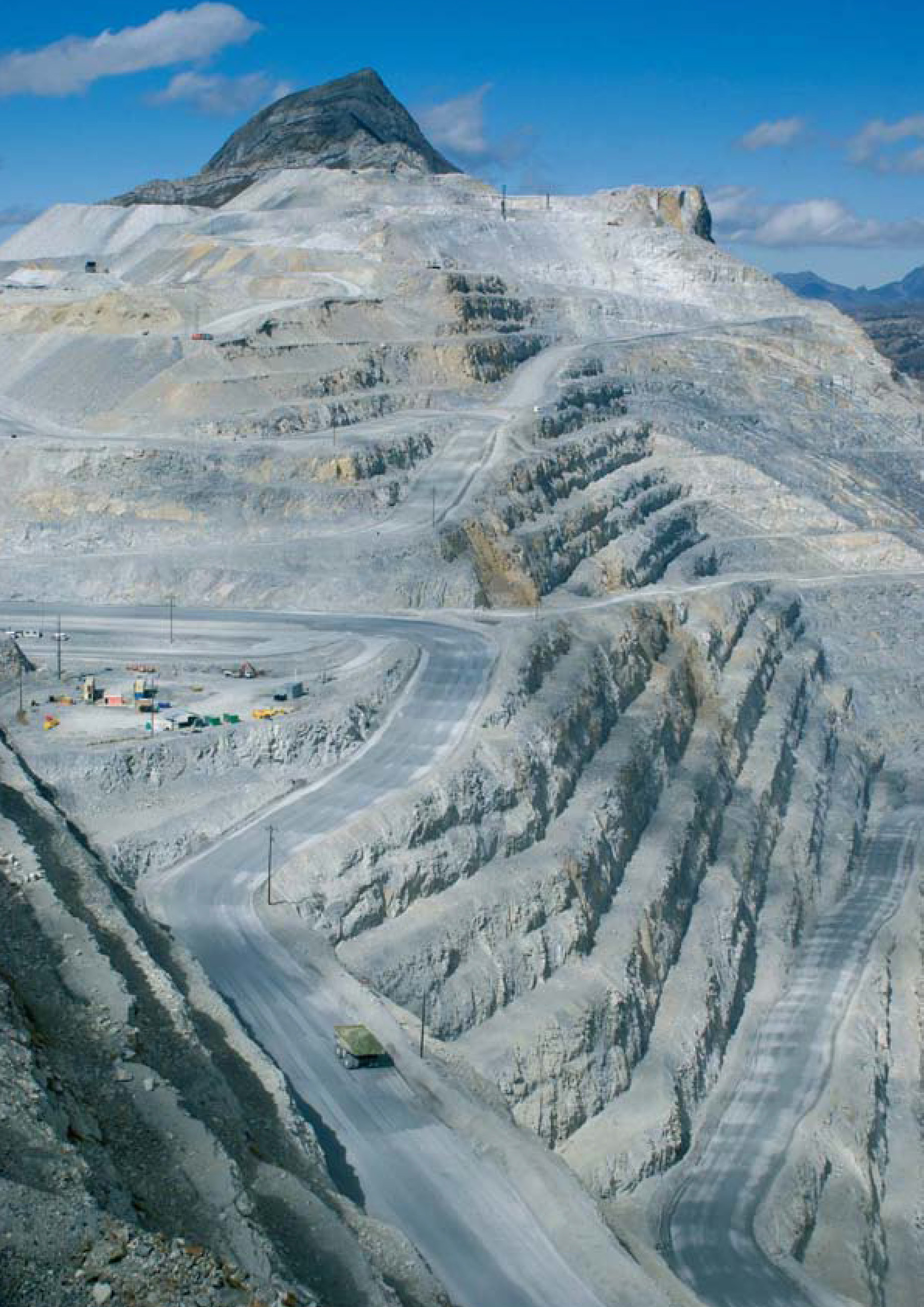
Comparing the results from a major ore characterisation campaign, using JKTech’s licensed SMC Tests® against JKTech’s Database, it was found that at Antamina 70% of samples were “very soft”, 22% of samples were “medium to soft”, while the remainder were “hard to very hard”.
Blast fragmentation data showed that fragmentation was driven more by ore competency than blasting practices. Comparison of powder factors and fragmentation data to JKTech’s Database showed that the powder factor was already very high, and that fragmentation was very fine when compared against similar rock types. Blast fragmentation was therefore not the real issue at the mine.
Soft ores tend to produce finer blast fragmentation producing lower mill residence times, hence lower SAG mill fillings (and subsequent accelerated liner wear), coarser grind size and overall lower metal recovery in the flotation circuit.
A review of SAG milling operations showed that, while processing the softest ore domain over a two-year period, the SAG mills operated with very low mill fillings ranging from 15% to 20%. This is very low considering ball charges ranged from 13% to 17%.
At Antamina, improving blast fragmentation alone while maintaining the current blending practice, would magnify this existing problem. This was shown through highly monitored ore campaigns where the material had significant fines. While finer fragmentation resulted in slightly higher throughput, it subsequently resulted in lower SAG mill power utilisation, less fines generated in the SAG mill and a coarser final grind size.
It was determined that more regular and accurate hardness information, along with head grade and flotation response information, would assist Antamina to implement more effective blending practices, ensuring a more homogeneous feed to the comminution circuit, bringing throughput stability and a more consistent final grind size, thereby enhancing flotation recovery. This could result in an extra $15M per year of revenue.
In line with JKTech’s Database, the six highly monitored blast trials also exhibited strong correlations between blast fragmentation and the Axb values from ore characterisation tests. As a result, JKTech proposed new blast domains based on rock competency with blast design recipes for each to allow better informed blending practices to stabilise the operation.
It was estimated that the new recipes would provide ~US$8m savings in blasting operations costs per annum.
While the above would take time to coordinate and implement it was determined that there was another processing improvement that could be achieved quickly. This would involve opening-up the primary crusher CSS and turning-off the pebble crushers to increase SAG mill filling while treating softer ores. This would represent an immediate increase in revenue estimated at ~US$1m per annum.
Immediate
US1m
per annum
potential revenue increase via crushing circuit adjustment
Medium Term
US8m
per annum
potential savings in blasting operations costs
Long Term
US15m
per annum
potential revenue improvement from increased recovery
Conclusion
JKTech’s JK Mine-to-Mill study at Antamina demonstrates that blast fragmentation is just one of the levers that can be adjusted to optimise the mine value chain. In this case study we demonstrate that while blasting optimisation is key to generating value in the mine value chain, in the right circumstance, an appropriate ore blending strategy can unlock as much or more value.
Additional Information
Research conducted at the Sustainable Minerals Institute (SMI) at the University of Queensland (UQ), has resulted in the development of methodologies and technology tools to address the various aspects of JK Mine-to-Mill. JKTech makes the following tools available to the industry through its consulting services and industry partners:
- The JK Drop Weight Test and the SMC Test® are the industry standard tests that capture the variations in ore competency from blasting and SAG milling; with the JKTech Database showing good agreements between Axb, blast fragmentation and SAG mill throughput. As the proprietary licensee of the tests, JKTech can offer more value for your money. Additionally, new rapid tests are being made available that will reduce the overall costs of ore characterisation programs.
- The JK Value-Based Ore Control (JKVBOC) software uses numerical modelling to simulate and predict the blast-induced 3D displacement of blasted material including the ore/waste boundaries so that ore loss and dilution can be measured and minimised.
- The JK Mill Filling Inference Tool (JKMillFIT) is a soft sensor that infers the SAG mill filling in real-time, integrating the mill power and ball/liner wear rates models. It is well established that mill filling drives SAG power, throughput and fines generation, hence the importance of providing mill operators with a high-resolution indication of SAG performance and their real operating limits which can be used to redesign the process control strategy, and to monitor plant response to the current ore blending practice.
- JKSimMet & JKSimFloat are industry leading software packages for the design and optimisation of comminution and flotation circuits.