Advanced Experimental Design
at Boyne Smelters Limited
JKTech partnered with Boyne Smelters Limited (BSL), Australia’s second-largest aluminium smelter, to identify strategies to improve the performance of their dry, fixed-speed autogenous (AG) mill.
Production activities at Boyne Smelters Limited include manufacturing carbon anodes in the carbon plant, aluminium production (smelting) in reduction lines, and casting of molten metal into aluminium products ready to ship.
BSL Operation Snapshot
Production:
More than 500,000 tonnes of
aluminium per year.
BSL Joint Venture Partners:
Rio Tinto, YKK Aluminium, UACJ Australia, Southern Cross Aluminium, Ryowa Development (I & II), and Sumitomo Chemical.
Location:
Boyne Island, Queensland,
Australia.
The Challenge
The AG mill product, which is used as an anode cover that provides an insulating barrier and allows the thermal balance of reduction cells to be controlled, was excessively fine and therefore ineffective at dissipating heat. As the mill was dry, fixed speed, autogenous and in open-circuit, conventional process variables typically used to control product sizing were unavailable as operational levers. The air velocity across the mill was also already set to its maximum limit.
A unique challenge was in the absence of any relevant historical data (even circuit throughput) due to the lack of instrumentation in the circuit. Therefore, historical trends could not be used to guide improvement strategies, and data needed to be generated from scratch (via properly-designed experiments) as part of the engagement.
The JKTech Solution
JKTech collaborated with the BSL team to design a plan that would establish the effect of two key controllable variables – feed blend and mill power draw – on product sizing.
Methodology
A key facet of the project was the desire to limit the capital spending that would normally be considered to prevent the overgrinding of feed.
A series of experiments were undertaken to better understand the effect of key variables upon the AG mill product sizing.
The experiments were planned as a central composite rotatable design (CCRD) that would enable multiple parameters to be tested simultaneously. This reduced the size of the experiment while also allowing for the effect of these parameters to be established amidst the inherent process ‘noise’ that would otherwise overwhelm the results of an ad-hoc plant trial.
Parameter tested 1: Feed A % (recycled cover)
Parameter tested 2: Feed B % (recycled cover from used carbon ‘butts’)
Parameter tested 3: Mill power draw (kW)
Results
The results of the experiments indicated that reducing excessive fines production could be achieved by targeting certain feed blends, while maintaining high mill power draw set points. An unexpected finding was in the effect of tramp metal accumulating in the mill over time. The experimental design allowed for this effect to be statistically disentangled from the other process variables, and established that tramp metal was the strongest driver of excessive fines production (since it behaved like grinding media). This finding prompted a review of mill maintenance practices, since more frequent removal of tramp metal from the mill was the most effective strategy to reduce fines production without any capital spending.
The success of the identified strategies was validated by post-trial monitoring indicating that the AG mill discharge successfully coarsened, as measured by the % of +500 µm material in the grind product (Figure 2). This was achieved without any CAPEX or engineering changes that would usually be considered to achieve the same result (e.g. pre-screens to allow fines to bypass the mill).
The project exemplifies how properly designed experiments can identify hidden potential in processing circuits, thereby mitigating the need for upgrades with capital expenditure.
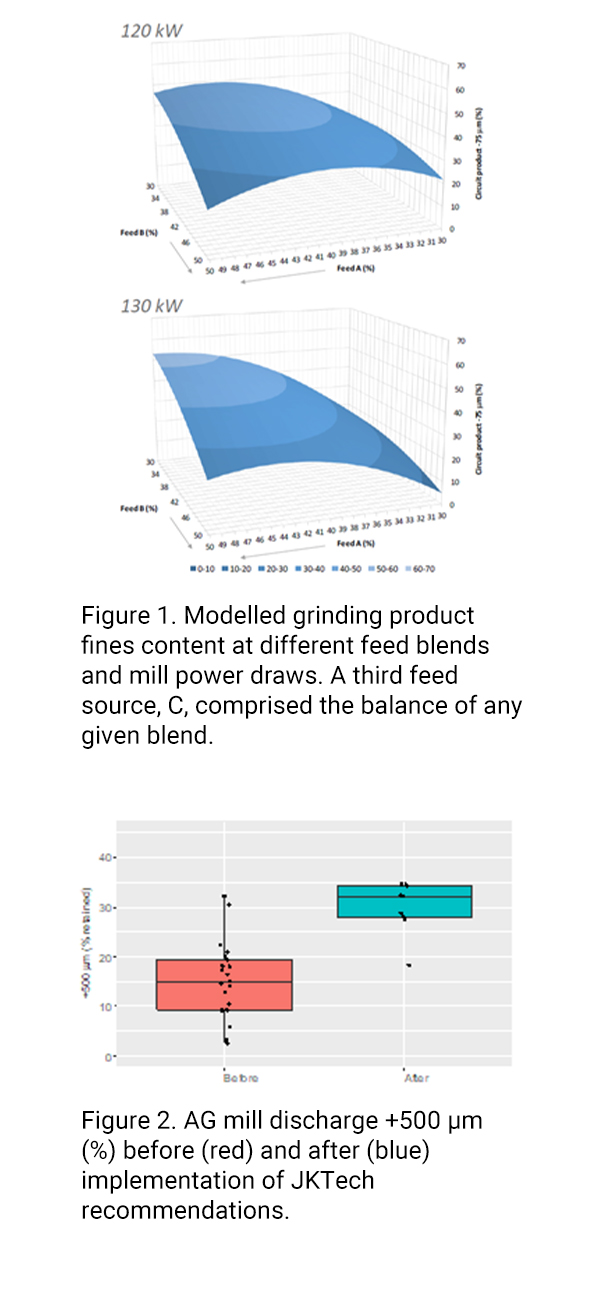